Transforming Energy for America
Manufacturing
We design reliable transformers engineered to last 60 years, delivered and installed in a timely manner, then monitored and serviced with longevity in mind.
A reliable transformer requires a robust design and a flawless execution based on our manufacturing pyramid. At the core are people, supported by modern facilities and equipment, a proven process, and flawless shipping and installation.
- Trained and certified technicians working under experienced supervision
- Modern, clean factory and state of the art equipment
- Error-free manufacturing and assembly of core, coils, and tank (internal and external)
- Accurate and error-free testing
- Flawless shipping and installation
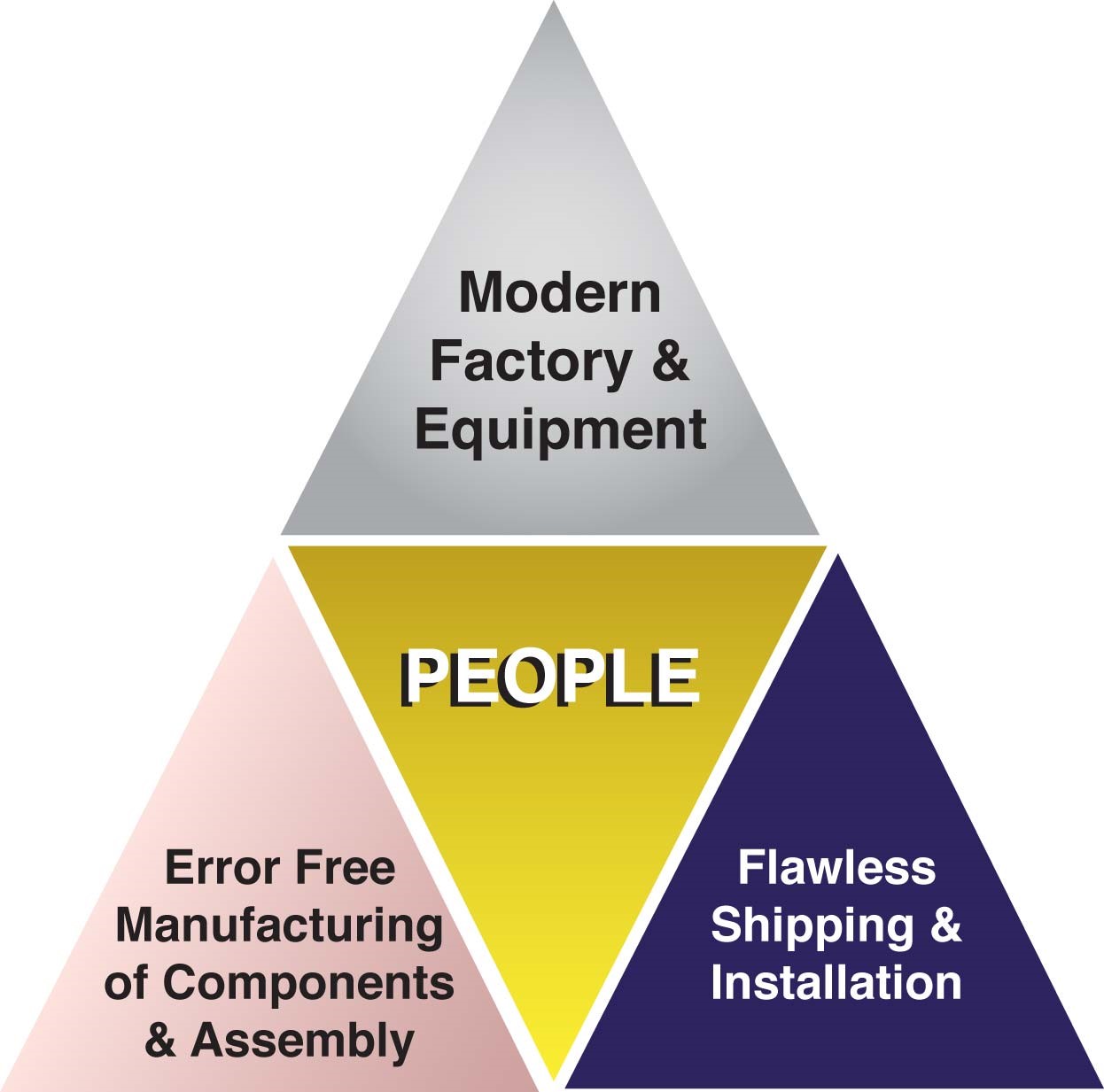
At the core of VTC's execution pyramid is our people - trained and certified technicians, professional oversight, and receiving tools and materials in a timely manner - all of which allow our team to perform at their best.

Trained & Certified Technicians
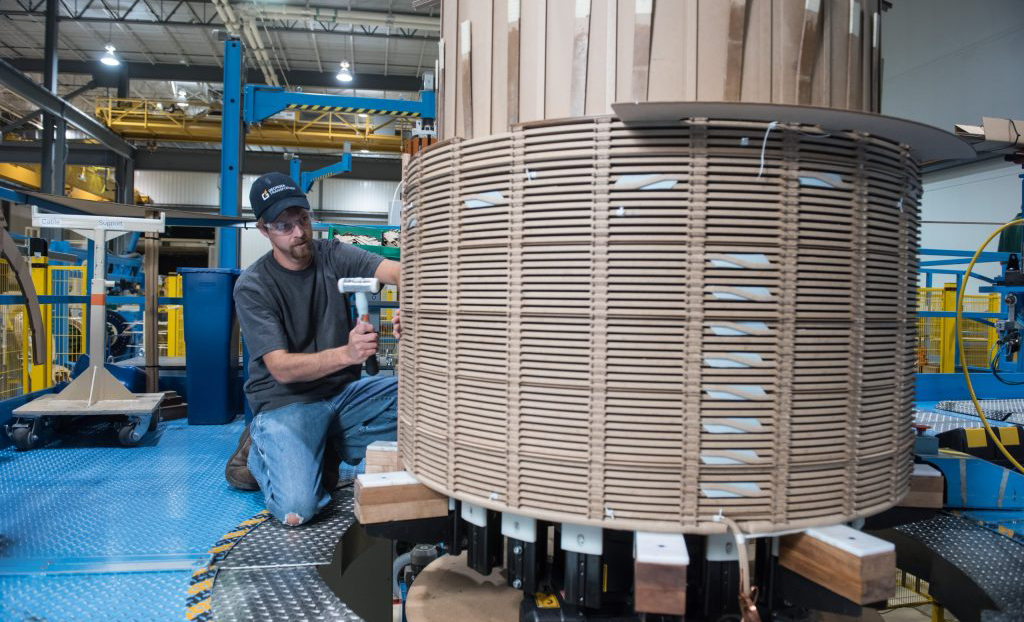
Professional Oversight
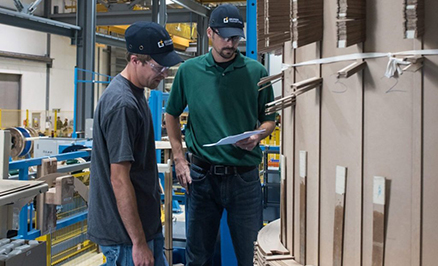
Our technicians are essential to the process and their training must be continuous and current.
Experienced supervisors are continuously overseeing and analyzing the product and the process from all angles to ensure efficiency and effectiveness. We also have a dedicated team in place to prevent process interruptions because of late or missing tools and materials.
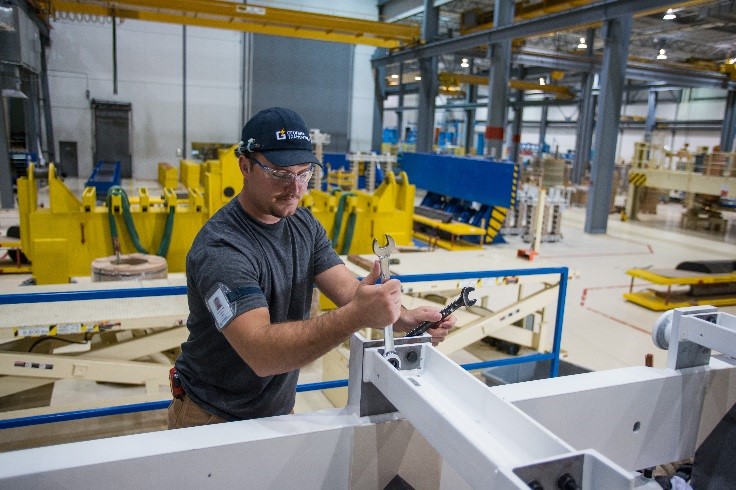
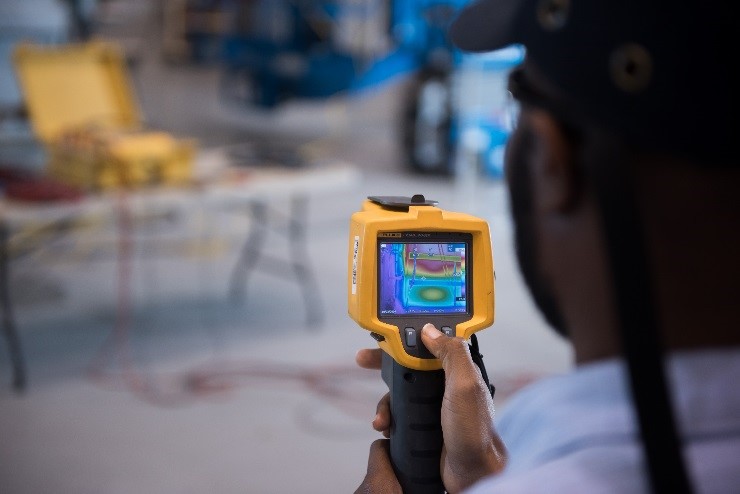
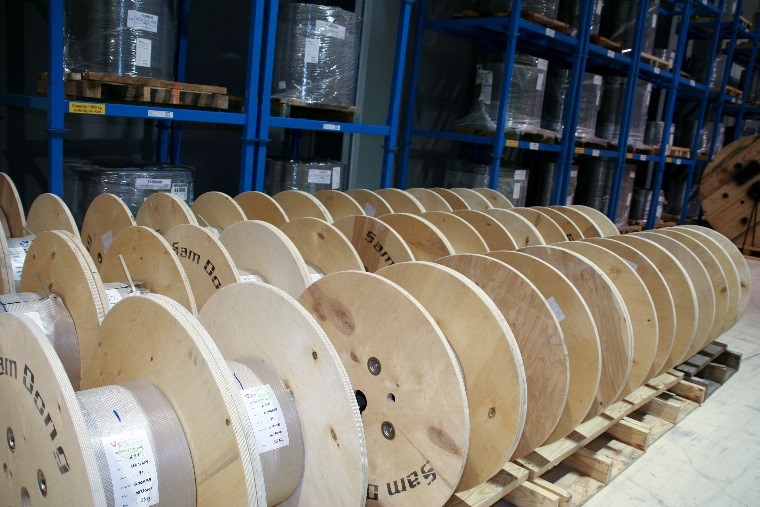

VPD
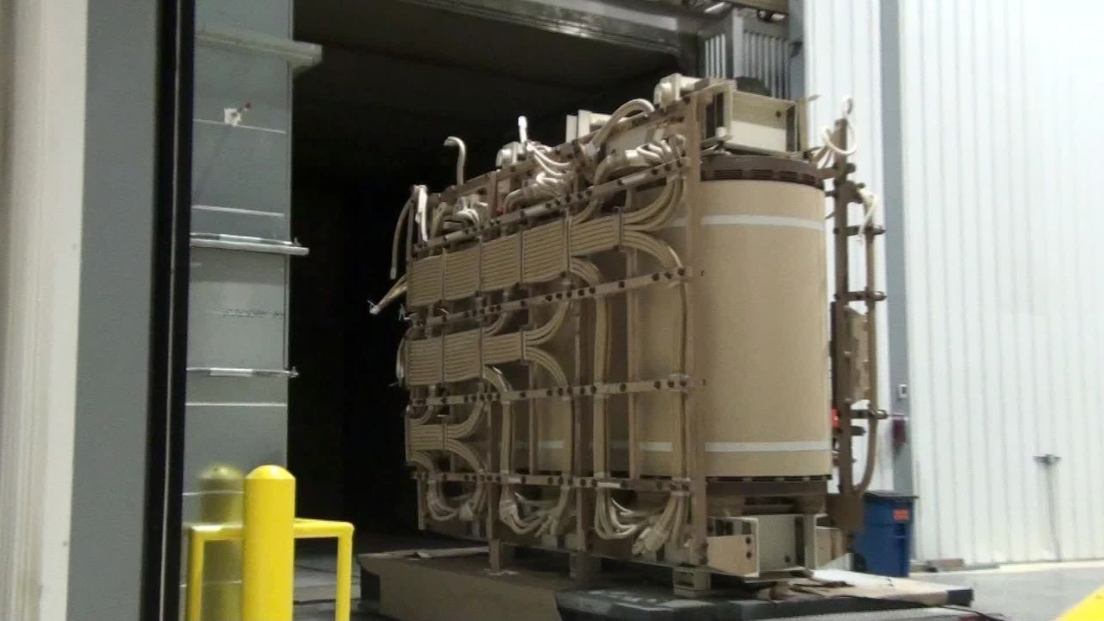
Process Summary
VTC employs a vapor-phase drying (VPD) process to completely extract moisture from the core and the coil. Final dry out begins by loading the entire core and coil assembly into one of our vapor phase vacuum chambers. The cycle begins by removing the majority of oxygen from the atmosphere of the chamber. At this point, solvent vapor is introduced which beings to condense on the core and coil. As the vapor condenses, it transfers its latent heat which results in a consistent and even heating of the transformer internal assembly.
Once process temperatures have stabilized, the system begins its high vacuum cycles, further reducing the pressure below 0.5 torr. Moisture removal begins during the heating cycles and progresses through the remaining vacuum cycles.
The chamber is then flooded with transformer oil to impregnate and seal the pores of the insulation materials and prevent further moisture absorption.
The core and coil are removed from the chamber for processing. After a thorough inspection, the assembly unit is immediately tanked and covered with transformer oil to inhibit moisture absorption. The oil is again drained, and the transformer is placed on high vacuum to remove any surface moisture. The transformer is once again vacuum-filled with hot, processed transformer oil for its final impregnation. After the appropriate sit time, electrical testing begins.
The VPD process provides many advantages in the manufacturing of power transformers. Reduced oxygen levels minimize oxidation and thermal aging of materials, and its excellent heating characteristics transfers heat to all parts of the core and coil assembly uniformly, quickly, and more efficiently than can be achieved with hot air or radiation processes.
All of our facilities are equipped with VPD ovens. Our Rincon, GA plant has three independent 430.5 sq ft (13345 cubic foot) ovens for large and extra-large power transformers. Each oven is PLC-operated to allow for precise temperature, vacuum, time control, and adjustable isostatic pressing of the transformer winding to ensure proper calibration and sizing of the coils.
If a transformer is too large for VPD, then a hot oil spray (HOS) method is used for drying. In this method, the transformer is placed under the vacuum and sprayed with heated transformer oil to remove moisture. HOS is continued until the desired moisture levels are achieved.

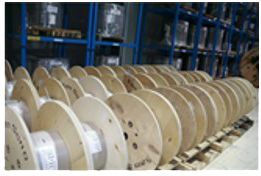
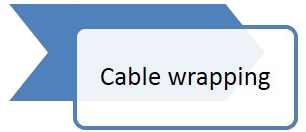
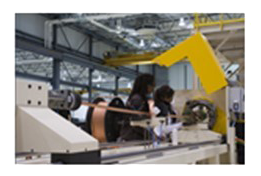
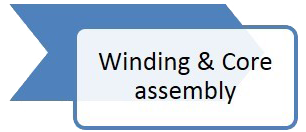
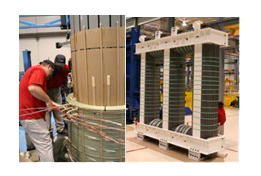
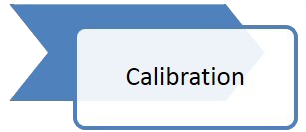
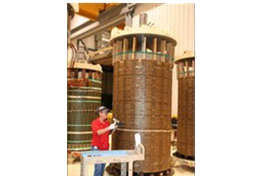
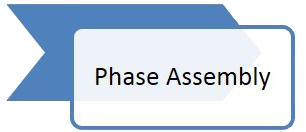
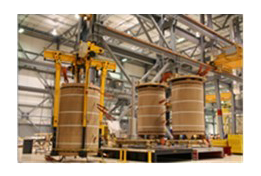
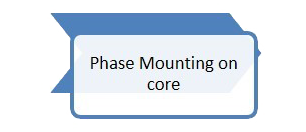
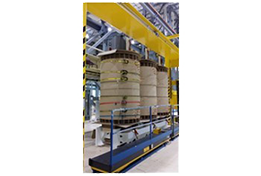
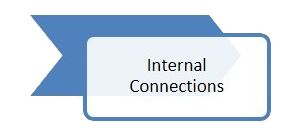
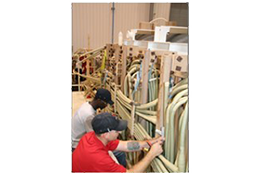
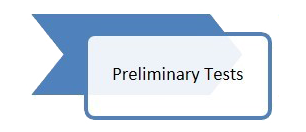
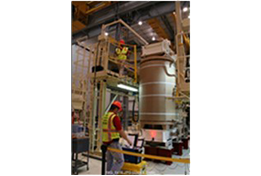
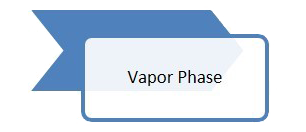
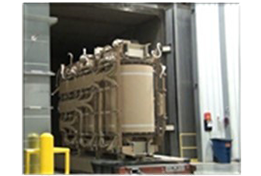
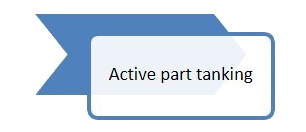
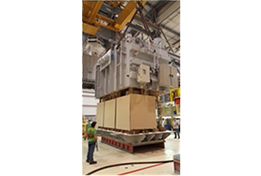
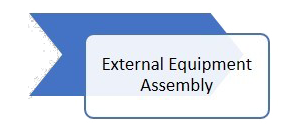
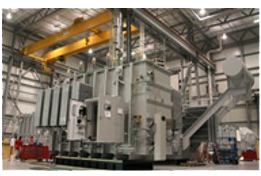
The above graphic demonstrates a typical flow of assembly at VTC’s Rincon plant, Georgia Transformer Corp. Processes at the other plants are essentially the same but vary depending on the size of the transformers.
Our processes have several built-in checks and balances to minimize errors. We have determined 11 critical hold points (HP) which stops the process for approval before recommencing. We have two additional control points where the team leader will analyze and review the finished work from different angles to make sure everything is correct for the final product. A traveling binder documents the inspection work for later analysis.