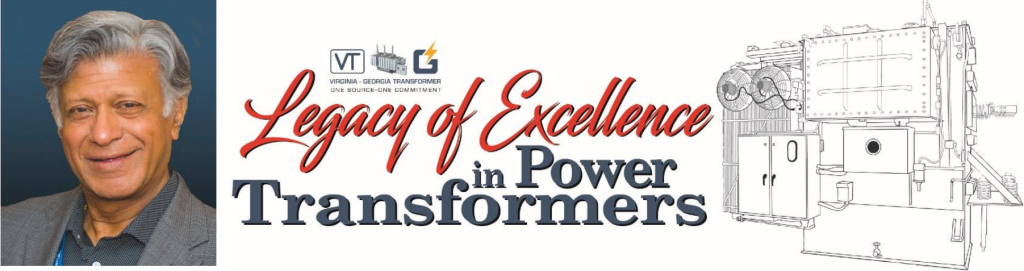
FLAWLESS EXECUTION
We have grown at an average rate of 15% per year since 1982 and we are continuously adding people at all plants.
By year 1990, we were little over 100 employees. Shop leadership was hands-on interacting directly with engineering under my personal supervision. We then produced units up to 10 MVA. In the 90’s we grew to over 300 people. We started a training shop in early 90s which we called BAT – Build A Transformer. A Transformer Circa was assembled and disassembled to give hands-on training to operators.
In the early 2000’s, we initiated on-boarding & training programs where operators were trained in five (5) basic skills of crimping, brazing, sealing, torqueing and painting. In the same decade a Fit and Finish (FF) function was established to reduce the defects on the product.


FIELD DEFECTS
By the year 2010, we were building up to 100 MVA / 230 kV size units. We realized that a reliable product requires Six-Sigma process control. We started assigning the experts in each department. These experts were called Technicians, their focus was on training and product quality thru process assurance.
A unique idea of All Technician work forces was born out of necessity in order to raise the process assurance.
Did you know that our FPY (First Pass Yield) is > 98% and RTS (Ready to Ship on time) is > 95%! What is our secret?

Let me share how we do it:

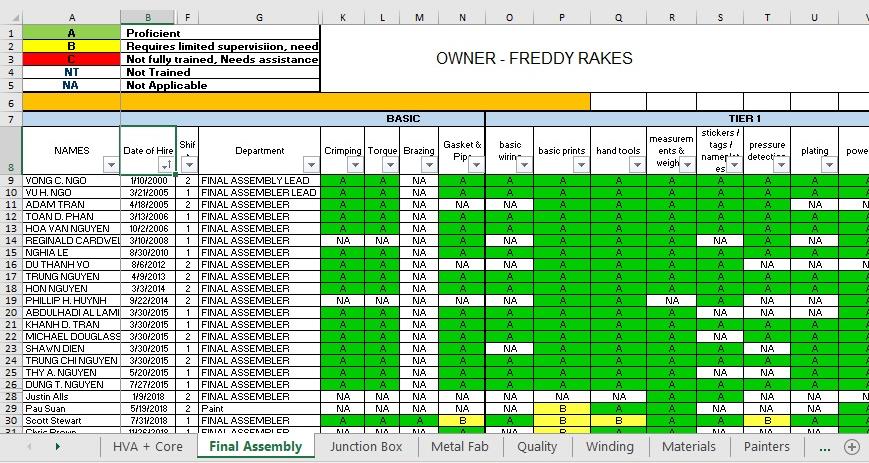
Smart Scheduling system accounts for the special feature such as 2 DETC and Smart Quality system adds special check points for the features.
Development of technical work force: Selected operators are trained in the technology of transformer for 30 days to launch on their path to become technician. These graduate of L3 program are trained in all departments, and while training are given the knowledge of shop technology to deliver the intent of the design.…… Flawless execution is the key to our success!
Circa 1990’s

Circa 1991, early quality inspection

Circa 2003

Circa 2003

Circa 2017

Circa 2019
